High-strength pultruded thermoplastic composites made of new raw material
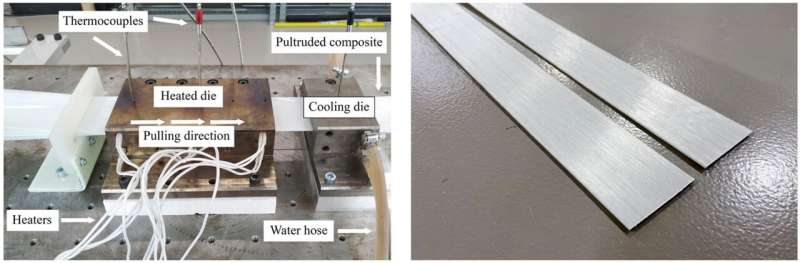
Skoltech researchers have enhanced pultrusion—a technology used to produce fiber-reinforced polymers of constant cross-section—profiles. These are light and stiff composite materials made of plastic and glass or carbon fibers. They do not rust, can be welded, are suitable for recycling, and could someday replace steel and aluminum in civil engineering, marine construction, and elsewhere. For now, they are mostly produced and examined in scientific laboratories. The findings of the study, which featured students from the Letovo boarding school for gifted children, are reported in Composites Communications.
Thermoplastic pultrusion involves pulling tapes of glass fibers impregnated with plastic through a machine where the plastic melts and the material assumes the desired shape.
Instead of the conventionally used source tape, the Skoltech team from the Center for Materials Technologies led by Assistant Professor Alexander Safonov, who heads the Institute's Laboratory of Composite Materials and Structures, used the kind of raw material usually employed in another manufacturing technique, resulting in a surprising 20% to 27% increase in the strength of the pultruded composites.
"Rather than using the more conventional tapes, we commissioned sheets of similar composition from the Zhongji Company, China, and sliced them into strips suitable for the pultrusion machine," the first author of the study, Skoltech Ph.D. student Kirill Minchenkov, commented. "In fact, we tried both the tapes and the sheets with an equal proportion of reinforcing fibers, and the latter yielded composites that exhibited significantly better mechanical properties. Namely, they showed higher compressive, tensile, and flexural strengths."
This is the first time these so-called preconsolidated sheets have been used in pultrusion to produce flat laminates.
The researchers attribute the better characteristics of their composites to the fact that sheets are thinner than tapes, allowing them to soak in the polymer better. This results in fewer pores and other defects in the composite, endowing it with superior properties.
Since the polymer component in the composite manufactured at Skoltech is polypropylene, the material is not only light and strong but it is also suitable for welding and recyclable. "This has to do with the distinction between thermoset and thermoplastic laminates," Minchenkov explained. "In the former, the polymer component hardens once and for all, so you cannot reheat it to weld two parts together or recycle the product. Polypropylene is the material much of the food packaging you see in a grocery store is made of. If you try to set fire on it, it softens, melts, and flows so you can change the shape of the material and remove plastic from fibers. This is similar to what happens in welding and recycling."
As thermoplastic pultruded flat laminates become better in terms of their characteristics and more feasible to manufacture, they will be increasingly capable of competing with industrial metals, such as steel and aluminum, as materials for civil construction, shipbuilding, and more.
More information: Kirill Minchenkov et al, Effects of the quality of pre-consolidated materials on the mechanical properties and morphology of thermoplastic pultruded flat laminates, Composites Communications (2022).
Provided by Skolkovo Institute of Science and Technology