August 25, 2017 report
New way to make steel that is both stronger and more ductile
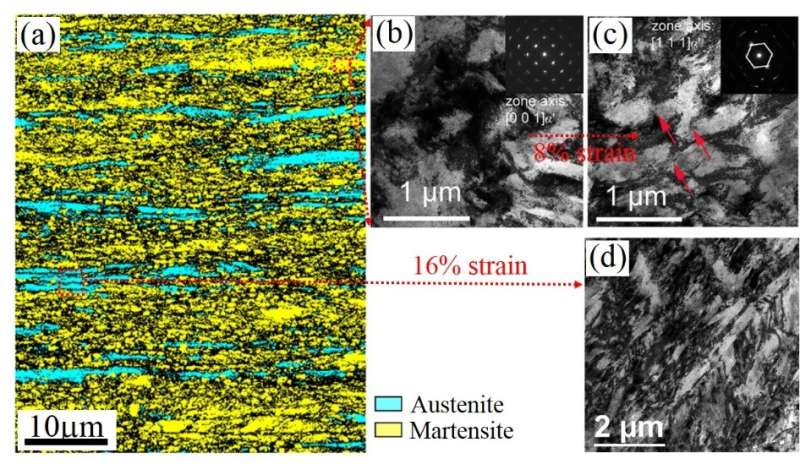
(Âé¶¹ÒùÔº)—A team of researchers from several institutions in China and Taiwan has developed a new way to make steel that offers more strength and ductility. In their paper published in the journal Science, the team describes part of the process and the ingredients that went into making the new type of steel and suggest possible applications.
As the researchers note, there are many industrial applications based on steel that require a high degree of strength and ductility (the ability to be pulled or deformed without breaking)—the higher degree of both, the better. But traditional steel-making techniques generally require a tradeoff: More strength means less ductility, or vice-versa. In this new effort, the researchers report that they have found a way around this problem.
To make the new steel, the researchers developed a new technique they call deformed and partitioned (D&P)—they cannot give all the details, of course, because that would prevent them from capitalizing on what they have created. But they do divulge that it belongs to a class of metal that the industry has defined as "breakthrough steels," which are medium manganese steels that are made with 0.47 percent carbon, 10 percent manganese, 0.7 percent vanadium and 2.0 percent aluminum.
They report also that the process involves cold rolling, which is followed up by tempering in a low temperature environment, and that metastable austenite grains are embedded somewhere in the process—this, they note, helps retain ductility while allowing for controlled defects that give the metal its strength. The group claims that the result is a steel with a yield strength of 2.2 GPa and 16 percent uniform elongation, which would make it the best in its class. They suggest the desired properties are due to the type of matrix formed during the rolling and tempering process.
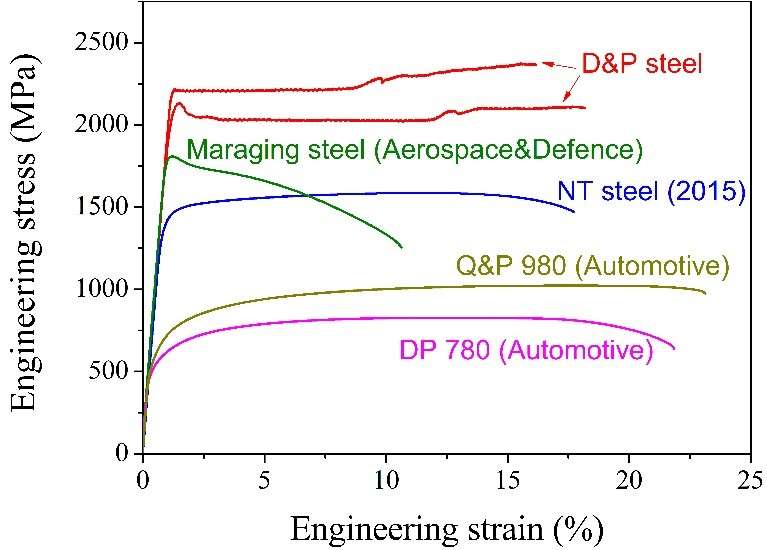
In addition to offering both more strength and ductility, the steel is also cheaper to make than other steels that are used in critical applications such as airplanes and rockets—the team claims that it can be made for just a fifth the cost of other more traditional methods. They also note that the process they developed offers the same desirable characteristics of other alloys.
More information: B. B. He et al. High dislocation density–induced large ductility in deformed and partitioned steels, Science (2017).
Abstract
A wide variety of industrial applications require materials with high strength and ductility. Unfortunately, the strategies for increasing material strength, such as processing to create line defects (dislocations), tend to decrease ductility. We developed a strategy to circumvent this in inexpensive, medium Mn steel. Cold rolling followed by low-temperature tempering developed steel with metastable austenite grains embedded in a highly dislocated martensite matrix. This deformed and partitioned (D&P) process produced dislocation hardening, but retained high ductility both through the glide of intensive mobile dislocations and by allowing us to control martensitic transformation. The D&P strategy should apply to any other alloy with deformation-induced martensitic transformation and provides a pathway for development of high strength, high ductility materials.
Journal information: Science
© 2017 Âé¶¹ÒùÔº